|
|
|
|
|
|
|
|
|
|
|
|
|
|
|
|
|
|
|
|
|
|
|
|
|
|
|
|
|
|
.gif) |
|
 |
|
 |
|
 |
|
.gif) |
|
|
|
|
|
|
|
|
|
|
 |
|
|
 |
|
|
 |
|
Measuring Engine Power
|
|
|
|
|
|
There is infact no way of directly measuring power - all types of dynamometer measure torque and then power is calculated from the formula BHP= Torque (ft/lbs) x rpm/5252. This basic equasion is the cornerstone of all engine design and development work.
Two main methods of measuring power are used in the automotive industry - (1) measurement at the crankshaft of the engine or (2) measurement at the driving wheels. We'll look at both of these seperately.
|
|
Engine Dynamometers
|
|
|
|
|
|
If we want to know the power of the engine alone then an engine dynamometer (or dyno) is used.
This is how nearly all manufacturers rate the output of car engines. The engine is bolted into a cradle and connected to the dyno - usually with a prop shaft which bolts onto the back of the crankshaft (or the flywheel). The power figures measured in this way are therefore usually called "flywheel power". The dyno is essentially a "brake" which can apply a known torque (or "load") to the engine.
When the engine is holding a stady spped under a given dyno load then the torque being applied by the dyno must be exactly equal to the torque being produced by the engine. If this were not so then the engine would either accelerate or decelerate.
Let's say we want to know the engine torque at 3,000 rpm. The throttle is gradually opened and at the same time the load applied by the dyno is increased
|
|
|
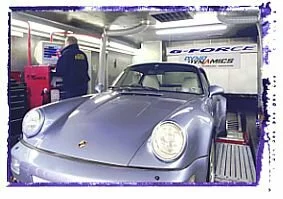 |
- eventually we get to the situation where
the throttle is fully open and the rpm is
steady at 3,000. The torque being applied
is written down and then the operation
would be repeated at say 4,000 rpm.
Soon we get a complete chart of torque at
all engine speeds. Of course we could also
measure part throttle power if desired.
Modern dynos are computer controlled and
can generatepower and torque curves very
rapidly without the operator having to manually adjust throttle and load controls.
|
|
They can be programmed to measure every so many rpm, say in 250 or 500 rpm steps - or they can measure a continuous torque curve while the engine accelerates at a preset rate. This can be used to simulate how the engine would actually operate in a particular gear when installed in the car.
There are various ways in which the dyno load can be applied. Older dynos use a hydraulic system with a rotor inside a water filled cavity - rather similar to the torque convertor in an automatic gearbox. Modern dynos generate the load with large electric motors. Even a simple friction disk or drum brake will work fine and this is where the name "brake" in Brake horsepower came from.
The important thing is that the load is able to be measured accurately and that there are no frictional losses in the system that escape measurement.
In order for dyno results to be comparable and universally understood there are a number of things that need to be closely controlled during the measurement process: Operating Conditions - air temperature, pressure and humidity affect the amount of power and engine produces. Cold dense air means a greater mass of oxygen per power cycle and thus more power is generated (provided of course that air/fuel mixture is properly calibrated for conditions prevailing).
There are formulae that can be used to calculate how much the measured power would change if the test condidtions were different. This enables dyno results to be "corrected" back to standard conditions to enable comparison with anyone else's test results. Sadly however there is no one universally accepted set of "standard" conditions because different automotive bodies in different countries use different standards to calibrate to.
"SAE" power standards are used in the USA and sometimes in England. "DIN" standards are used on the continent and there are a few other oddball systems just to confuse the issue. So just because your car is rated at 100 bhp and a friends at 110 bhp doesn't necessarily mean that his engine is more powerful - it depends whether both measurements were corrected to the same standard conditions.
One of the tricks we've seen used to get bigger "corrected" bhp numbers is to use a very high ambient temperature reading for the dyno test. If the operator measures the temperature close to the engine rather than well away from it then obviously he will get a reading that is much higher than ambient. When the bhp numbers are corected back to a lower standard ambient air temperature they will increase. I saw an engine dyno sheet the other day where the ambient air temperature in February, in England was supposedly 37 degrees C. Now either that test was done with the temperature probe sat right on top of the engine or it's a part of country we don't yet know about where we would very much like to live!!
|
|
Rolling Road Dynamometers
|
|
|
|
|
|
Also called chassis dynometers, these are used to measure power at the driving wheels. This avoids the inconvenience of having to remove the engine to test it if a tuning modification has been made. However, it means that the power figures obtained will be lower than the flywheel power because of the frictional losses in the drivetrain and tyres. This leads to one of the biggest sources of confusion, error and plain misinformation in the tuning industry.
You see, as discussed above, all major manufacturers quote flywheel power so it is undrstandable that people want to know if the hard earned cash they have spent on performance upgrades has increased the power of their engine and by how much. To know this for certain means knowing how much the transmission losses are. There is enormous pressure on rolling road operators to be able to quote flywheel bhp rather than wheel bhp and most operators now run proprietary software systems which supposedly print out "flywheel" power figures.
These software systems are useful for estimating factory performance figures. However, in our experience, as engine performance is increased their "flywheel" figures generally become unreliable. We know the majority of other rolling road tuners in this country quote "flywheel" figures and here's us saying it is irrelevant. So we'd better explain some more and then you can make your own mind up.
|
|
|
|
|
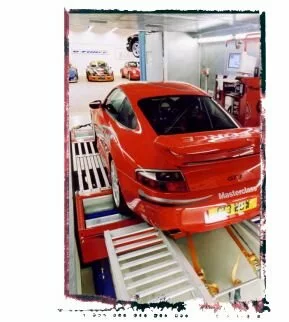 |
How a rolling road (chassis Dynamometer) works |
|
|
|
|
The car is driven onto a rig so that the driving tyres are resting between two steel rollers. The torque is measured at different speeds in exactly the same way as the engine dyno works except that it is torque at the rollers rather than torque at the flywheel. The braking load is applied to one of the rollers by either a hydraulic (water brake) or electrical system again in just the same way as the engine dyno would apply a torque to the cranksharft of the engine.
The same universal equation at the top of the page can then be used to calculate bhp at the rollers by knowing the torque and the rpm of the rollers (NOT the rpm of the engine at this stage) - but if the engine rpm is measured simultaneously then we can know roller bhp at a particular engine rpm.
The BIG problem with all this is if any tyre slip is taking place. Remember most of these other rolling
|
|
road tuners use smooth steel rollers, which over time get quite polished. How much grip do you think you would get if roads were made of polished steel rather than tarmac? The effect of tyre sleep are complex but what we do know is that you can get some really strange bhp figures from highly tuned engines on narrow tyres and the readings are invariably too high not too low.
|
|
What is transmission loss?
|
|
|
|
|
|
All mechanical systems suffer from friction and a proportion of the power fed into a system will get dissipated by friction and turn into heat and noise. Note the key phrase there - "power fed into a system". For there to be a loss there must be an input. When your car is parked overnight with the engine switched off, the transmission losses are obviously zero. When the car is running then some proportion of the flywheel power will be lost in the gearbox, final drive, drive shaft bearings, wheel bearings and tyres.
For a given mechanical system these losses will usually stay close to a particular fixed % , lets say 10% for arguments sake, of the input power. So if the car is cruising and developing 20 bhp then 2 bhp will get absorbed as friction - under full power, say 100 bhp, then maybe 10 bhp will get absorbed.
Now it is true that not every component in a transmission system absorbs a fixed % of the input power. Some components like oil seals and non driven meshed gears (as in a normal car multi spped gearbox) have frictional losses which are not affected by the input torque. These losses do increase with speed of course but at a given rpm can be taken to remain constant even if the engine is tuned to give more power. We'll look at real world transmission loss percentages later.
The biggest source of loss in the entire transmission system of a car is in the tyres - they account for half or more of the total losses between the flywheel and the rollers. Each set of driven gears, i.e. the final grive gear of the particular gearbox ratio that you happen to be testing the car in, only absorbs about 1% to 2% of the engines power.
|
|
How do these systems that measure transmission losses work?
|
|
|
|
|
|
The power curve at the wheels is taken in the usual way as explained above. then, at peak rpm, the operator puts the car into neutral and lets the rollers slow down under the drag of the tyres and transmission. The software then measures this drag (or "coast down loss") as "negative" power and adds it to the wheel power to get back to the supposed flywheel power.
However - and hopefully you've spotted the problem now - the engine is not feeding any power into the drivetrain while the car is in neutral - in fact it isn't even connected to the drivetrain any more!! Whatever drag this is that's being measured it has nothing at all to do with the proportion of the flywheel power that gets lost as friction when the engine is powering the car in the normal way.
The engine could now be an 800 bhp F1 engine or a 30 bhp mini engine for all it matters because it isn't connected to the gearbox or feeding any power into it. Obviously this "coast down loss" is something to do with the transmission and tyres but it is not the true transmission loss - in fact this coast down loss should never be expected to change for a given car at a particular rpm regardless of how much you tune the engine whereas a true transmission loss will increase as the engine power increases because it is dependent to a large extent on the amount of power being fed into the transmission.
We've seen a car that over time was tuned from 280 bhp at the wheels to 335 bhp at the wheels and the "coast down loss" stayed the same for every power run to within a fraction of a horsepower - exactly as you would have predicted. As the engine was tuned to give more power the "true" transmission losses must have also increased to some extent but these chassis dyno systems don't, and can't show this happening.
|
|
Is it possible to measure the true transmission loss of a car?
|
|
|
|
|
|
Yes - only one - by measuring the flywheel power on an accurate engine dyno, the wheel power on an accurate chassis dyno and taking one away from the other. There is no way of finding out the true transmission loss just by measuring the power at the wheels.
So hopefully that's got you all thinking a bit more now instead of just taking for granted the "flywheel" figure you were given the last time you took your car to the rollers.
Even worse is the fact that some of these software systems allow the operator to just programme in the % transmission loss he wants the system to add to the wheel figures.
|
|
What should you do when you take your car to a rolling road?
|
|
|
|
|
|
Firstly, make sure you get printouts that show the wheel bhp and not flywheel bhp. If you need to know the flywheel bhp then you will have to estimate it - there's no other way short of using an engine dyno.
The corrections you need to make for cars with manual gearboxes are these:
The average rear wheel drive road car with between 100 and 200 bhp loses about 17% of the engine bhp as transmissions losses. We find Porsche transmission losses are 12% and 18%, depending upon specific model and the age of the vehicle. We use 15% as a rule, and find the estimates of flywheel power compared to factory figures very reliable. 4-wheel-drive cars will have higher losses because of the extra differentials and other power transmission components.
A reasonable estimate of an average 4wd car's losses might be 22% to 25% of the flywheel power.
As a guide we have found using a transmission loss of 24% for Mitsubishi Lancer EVO's and Subaru Impressas to be very accurate. What your own specific car loses is anyones guess - yours is as good as mine - but it shouldn't be far fromt he figures above.
No car in the world loses anything like 30% of the engine's power in the transmission and tyres as many rolling road operators would try to have you believe. So take the wheel figure and divide by 0.85 for RWD and that will get you as close to the true engine bhp as you are ever going to know. A rule of thumb we use which is quite accurate is to treat the losses as being 12% of the flywheel power plus 10 bhp for RWD cars. This equation "loads" low powered cars more than high powered cars which is more closely like what happens in reality. Remember, these percentages are just good realistic averages.
The measured wheel bhp can change depending on tyre pressure, tyre size, suspension angles and other things which wont effect the flywheel power - so the actual transmission loss % will also change. For these reasons we try to standardize as many of these things as possible if we do a series of power runs over a period of time. We always use the same tyre pressure because this is a factor which can easily change from day to day.
As you tune a particular car, the losses won't increase exactly in proportion to the power because as mentioned above, some components in the transmission have fixed losses which are not dependent on engine power. However, neither you nor the dyno operator will have any real idea of exactly how the losses have changed so you might as well just continue to apply the percentages above to give some sort of realistic guide to the new flywheel bhp.
What sort of % transmission loss do these software systems show? - well for normal road cars up to 250 bhp, we've seen as high as 35% and as low as 10%. So take the same car with 150 bhp at the wheels to 2 different rollres and you might get anything from 165 bhp to 200 bhp being "predicted" as the flywheel figure. In reality 150 bhp at the wheels will be no more than about 180 bhp at the flywheel.
Another good way of bumping up the power figures on rolling road tests, as mentioned above under engine dynos, is by "playing about" with the air temperature and the pressure corrections. If you dial in your own "standard" conditions as being freezing cold with the barometer going off the scale, or you put the temperature probe near the engine, you can get the system to add huge amounts of power to what was actually measured. So make sure you know if such corrections were made or not and to what standards they were made if any.Plenty of rollers still just quote the measured figure because they don't have computer systems to do the calculations. Hopefully it should be apparent that 100 bhp is not just 100bhp and end of story. It depends how it was measured, where it was measured, what corrections were applied and of course whether the dyno was even accurate in the first place.
We don't get too excited when we see other people quote huge power outputs for their engine modifications. if our engines outperform theirs on the track then they can quote whatever power figure they like.
|
|
If you don't know how much power you have at the wheels -
you dont know how much power u have!!
|
|
%20animation%20frames/top%20section%20of%20animation(no%20logo).gif) |
|
%20animation%20frames/tech%20bottom%20animation.gif) |
|
%20animation%20frames/static%20middle%20slice%20of%20animation.gif) |
|
%20animation%20frames/tech%20bottom%20animation.gif) |
|
%20animation%20frames/static%20slice%20of%20animation%20(bottom).gif) |
|
 |
 |
 |
 |
 |
 |
 |
 |
 |
 |
 |
 |
 |
 |
 |
 |
 |
 |
 |
 |
 |
 |
 |
 |
 |
 |
 |
 |
 |
 |